工序交叉培训英语,究竟谁先谁后
- 作者: 胡星葵
- 来源: 投稿
- 2024-10-01
1、工序交叉培训英语,究竟谁先谁后
Crosstraining in Operations: Which Comes First?
In the fastpaced world of manufacturing, efficiency is key. Crosstraining employees in multiple operations can improve productivity, flexibility, and employee morale. But when it comes to implementing crosstraining, the question arises: who should be trained first, the more experienced or less experienced employees?
Arguments for Training Experienced Employees First
Increased productivity: Experienced employees have a deeper understanding of the overall process and can quickly adapt to new roles.
Improved quality: Their experience allows them to identify potential problems and prevent errors.
Enhanced mentoring: They can serve as mentors for less experienced employees, ensuring a smooth transition and knowledge transfer.
Arguments for Training Less Experienced Employees First
Increased agility: Less experienced employees are often more adaptable and open to new challenges.
Lower training costs: Training newer employees may be less expensive than retraining experienced employees.
Talent development: Crosstraining provides less experienced employees with opportunities for growth and career advancement.
Determining the Optimal Approach
The best approach depends on the specific needs and circumstances of the organization. Consider the following factors:
Current skill levels: Assess the technical proficiency and knowledge base of both experienced and less experienced employees.
Production demands: Determine if urgent production needs require immediate crosstraining of experienced employees.
Mentoring resources: Identify experienced employees who are willing and capable of mentoring less experienced colleagues.
Recommended Sequence
In most cases, a phased approach is recommended:
1. Identify experienced employees as mentors: Select individuals who are proficient in multiple operations and possess strong communication and mentoring skills.
2. Crosstrain less experienced employees with mentors: Pair them with mentors for onthejob training and guidance.
3. Gradually expand crosstraining to experienced employees: As less experienced employees gain proficiency, consider crosstraining experienced employees to enhance their versatility and succession planning.
By carefully considering the factors outlined above and adopting a phased approach, organizations can effectively implement crosstraining to maximize productivity, flexibility, and employee development.
2、工序交叉培训英语,究竟谁先谁后
CrossTraining in Operations: The Case for a FirstIn, FirstOut Approach
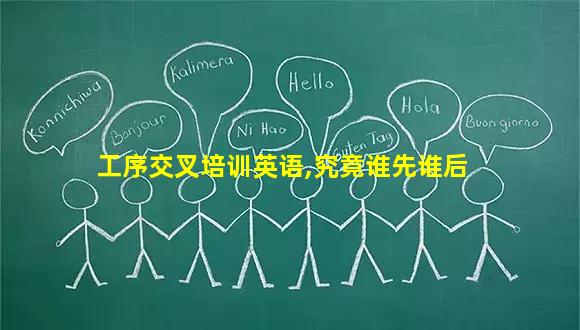
3、工序之间的联系与配合
工序之间的联系与配合
在生产过程中,工序之间存在着紧密的联系和相互配合。这种联系和配合对于保证产品质量、提高生产效率、降低生产成本具有重要意义。
联系方式1. 前后工序相依性
每个工序的生产都依赖于前一个工序,并为下一个工序提供原料或半成品。例如,在机械制造中,铸造工序完成后,才能进行加工工序;加工工序完成后,才能进行装配工序。
2. 影响范围的关联性
每个工序的变化都会对其他工序产生影响。例如,铸造工序中出现的缺陷,如果未被及时发现和修复,将导致后续的加工和装配工序出现问题。
3. 时间序列的连接性
工序之间具有时间上的先后顺序。例如,在装配线中,各个工位的工作顺序必须遵循一定的工艺路线,才能保证产品顺利装配完成。
配合形式为了实现工序之间的有效配合,需要采取以下措施:
1. 建立工艺文件
工艺文件详细规定了每个工序的工艺参数、操作步骤、质量标准等,为工序之间的配合提供了统一的技术依据。
2. 实行工序间协调
通过制定合理的生产计划和调度方式,协调不同工序的工作节奏,避免出现脱节或阻塞的情况。
3. 加强工序间沟通
工序之间的及时沟通对于及时发现和解决问题至关重要。可以通过定期召开工序协调会、建立沟通平台等方式,加强信息交流。
4. 完善质量控制体系
在每个工序结束后进行质量检查,及时发现和纠正问题,防止缺陷传递到后续工序。
5. 培养员工协作精神
增强员工的协作意识,营造良好的工作氛围,促进不同工序之间相互理解和支持。
效益工序之间的良好联系和配合可以带来以下效益:
提高产品质量提高生产效率
降低生产成本
缩短生产周期
改善工作环境